Railway ballast is an essential component of railway tracks that plays a crucial role in maintaining the stability and safety of rail operations. If you’ve ever wondered why trains can smoothly traverse vast distances without derailing, a significant part of the answer lies in the ballast beneath the tracks. This gravel-like material may seem unassuming, but it serves multiple critical functions, from bearing loads and providing drainage to minimizing vibrations and maintaining track alignment. Understanding railway ballast is crucial for appreciating how railroads function efficiently and safely.
This blog post will explore everything you need to know about railway ballast. We will begin by defining ballast and discussing the commonly used materials. We will also highlight the importance of ballast in providing resistance against loads and its crucial role in railway infrastructure maintenance. Additionally, we will cover specific details such as the typical ballast weight, its profile, and the maintenance practices that ensure its longevity and effectiveness. Whether you are a rail enthusiast, a student, or a professional in the railway industry, this comprehensive guide will provide valuable insights into the foundation of modern railroads.
From shaping shoulders to sweeping excess, our “ballast regulator” ensures a clean, stable, and efficient ballast bed.

What is Ballast in Railway?
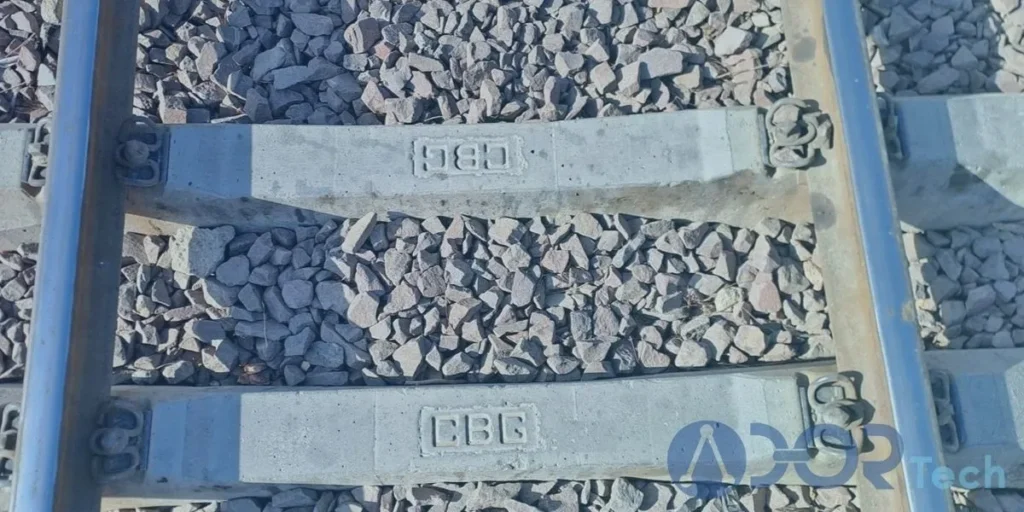
Railroad ballast consists of a layer of coarse, granular material positioned beneath and around railroad tracks. Its main purpose is to uphold the tracks and maintain their position when trains travel over them. Usually produced from crushed stone, gravel, or similar materials, ballast provides a secure base, aiding the even distribution of the trains’ weight across the track bed. This prevents the tracks from shifting and ensures a smooth and safe journey for trains.
Ballast is crucial for maintaining track integrity, especially in challenging weather conditions, by aiding drainage and preventing water accumulation. Furthermore, it helps minimize vibrations from passing trains, which can contribute to track and train wear and tear, thereby extending the life of the railway infrastructure.
The significance of railway ballast cannot be emphasized enough. Without it, tracks would be susceptible to movement and misplacement, resulting in possible derailments and safety risks. Furthermore, the upkeep of ballast is quite simple, making it a feasible option for maintaining and safeguarding railway tracks. Grasping the role and significance of ballast is crucial for anyone with an interest in the operations of railway systems.
See also: “Improved Method of Railway Ballast Maintenance“
Why is Ballast Used on Railways?
Ballast is a vital component of railway infrastructure, playing several key roles that ensure trains’ safe and efficient operation. Primarily composed of crushed stone, gravel, or similar materials, ballast is laid beneath and around railway tracks. Its main functions include providing stability, facilitating drainage, reducing vibrations, and distributing loads. By understanding why ballast is used on railways, we can appreciate its importance in maintaining the integrity and longevity of the track system. Below, we will explore the reasons for using ballast in more detail, covering stability and support, drainage, vibration reduction, and load distribution.
Stability and Support
Ballast keeps railway tracks stable and securely in place. Its weight and distribution prevent lateral movement and misalignment of the tracks, which is essential for safety. Properly maintained ballast ensures that the tracks remain in their correct position even under the heavy loads exerted by passing trains. This stability is crucial to avoid derailments and maintain smooth train operations.
Drainage
Adequate drainage is another critical function of railway ballast. The granular nature of ballast allows water to drain away from the tracks, preventing accumulation and potential water damage. Good drainage is vital for maintaining the integrity of the track structure, especially in areas prone to heavy rainfall or flooding. By keeping the tracks dry, ballast helps to prevent the formation of mud and the weakening of the railway foundation.
Vibration Reduction
The ballast also plays a significant role in reducing the vibrations caused by passing trains. These vibrations can lead to wear and tear on the tracks and the train components. The ballast absorbs and dissipates these vibrations, contributing to a smoother and quieter ride. This extends the life of the railway infrastructure and enhances the comfort of passengers and the efficiency of freight transport.
Load Distribution
Another essential role of ballast is loading distribution. Ballast spreads the load from the trains evenly across the subgrade, reducing the stress on any single point of the track structure. This distribution helps to prevent the deformation and failure of the track bed under the heavy weight of passing trains. By distributing the load effectively, ballast ensures the longevity and durability of the railway tracks, making it possible to handle the significant pressures exerted by modern trains.
Railway Ballast Material
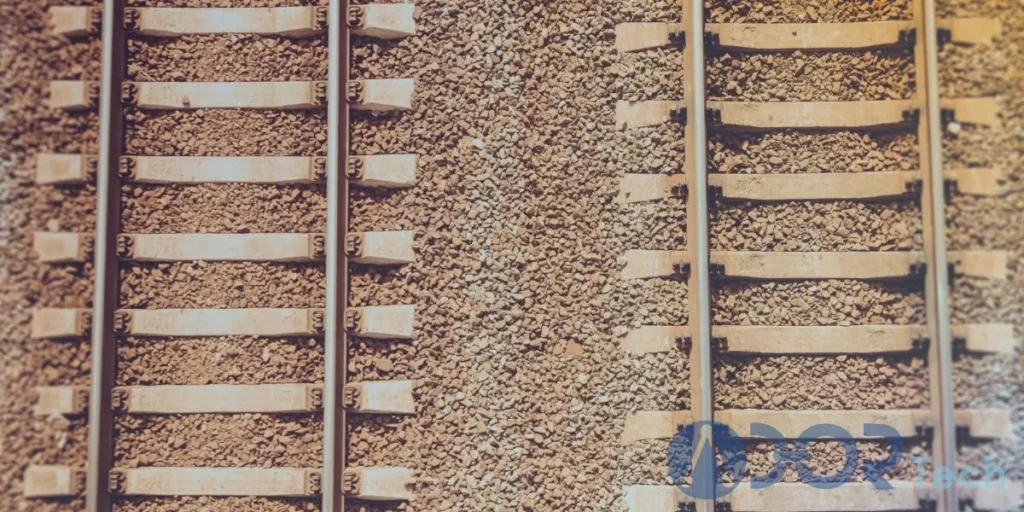
Railway ballast is typically composed of materials that provide the necessary support and stability for railway tracks. The primary materials used for railway ballast include crushed stone, gravel, and slag. These materials are chosen for their durability and ability to withstand the weight and pressure of passing trains. Each material has unique properties that make it suitable for use as ballast, ensuring the tracks remain stable and aligned under heavy loads.
Types of Materials
1- Crushed Stone: This is the most common material used for railway ballast. Crushed stone is selected because of its strength and angularity, which allows it to lock together and provide a stable base for the tracks. Granite and limestone are frequently used types of crushed stone due to their durability and resistance to weathering.
2- Gravel: Although less common than crushed stone, gravel is sometimes used in railway ballast. It consists of rounded stones that can also provide good drainage and stability. However, gravel is less effective than crushed stone in locking together, which can result in less stability under heavy loads.
3- Slag: Slag, a by-product of the steelmaking process, is also used as ballast. It has similar properties to crushed stone but can be more cost-effective. Slag is durable and provides good drainage, making it a viable alternative in some regions.
Properties of Good Ballast
1- Durability: Good ballast must be durable enough to withstand the pressure of passing trains without breaking down. Materials like granite and limestone are preferred for their high durability and resistance to crushing and weathering.
2- Hardness: The hardness of the ballast material is crucial in ensuring that it does not wear down quickly. Hard materials can better resist the constant abrasion from train wheels and environmental conditions.
3- Angularity: Angularity refers to the sharpness of the edges of the ballast stones. Angular stones lock together more effectively than rounded stones, providing better track stability. This interlocking property helps maintain track alignment and prevent shifting.
4- Size and Gradation: The size of the ballast particles should be consistent to provide uniform support. Typically, ballast stones are between 25-60mm in size. A well-graded ballast with a mix of sizes can fill gaps and provide better load distribution.
5- Drainage: Good ballast must have excellent drainage properties to prevent water from accumulating around the tracks. Materials like crushed Stone and slag, due to their porous nature, are particularly effective in facilitating drainage.
6- Cleanliness: Ballast should be free from dirt and other fine particles that can clog drainage and reduce effectiveness. Clean ballast maintains its drainage properties and longevity.
7- Non-degradable: The material should be chemically inert and non-degradable, meaning it does not react with water or other substances, which could cause it to break down or degrade over time.
Railway ballast can effectively support and stabilize railway tracks using materials with these properties, ensuring safe and efficient train operations. Understanding the types of materials and their essential properties is key to maintaining a reliable and durable railway infrastructure.
Railway Ballast Profile
1- Standard Profiles:
The standard cross-sectional profile of railway ballast on the track bed is typically triangular. This profile is designed to support the railway sleepers (ties) and evenly distribute the load. The ballast is laid to a specific depth, generally ranging from 150 to 300 mm, depending on the type of railway line and expected load. The profile starts from the base of the rail and extends outward and downward at an angle, ensuring that the ballast layer is well-compacted and stable.
2- Importance of Profile:
Maintaining the correct ballast profile is crucial for optimal track performance. A well-defined profile ensures that the ballast provides adequate support and stability to the tracks, preventing lateral or vertical movement. This stability is essential to keeping the tracks aligned and to prevent derailments. Additionally, a proper ballast profile facilitates effective drainage, preventing water accumulation that can weaken the track structure. Regular maintenance of the ballast profile helps distribute the loads evenly, reducing the wear and tear on the tracks and extending the lifespan of the railway infrastructure.
See also: “Ballast Regulator Machine Operating Principles“
Railway Ballast Weight
Railway ballast typically weighs between 1,600 and 1,800 kilograms per cubic meter, depending on the material used. This weight ensures that the ballast can effectively anchor the tracks and support the heavy loads passing trains impose. For example, a standard section of track with a ballast layer about 30 centimeters deep can weigh around 480 to 540 kilograms per square meter. This substantial weight contributes to the stability and robustness of the railway tracks, helping to prevent any movement or misalignment.
Several factors can influence the weight of railway ballast. The type of material used is a primary factor; for instance, granite and limestone are commonly used due to their high density and durability, contributing to the ballast’s overall weight. Additionally, moisture content significantly affects the weight of ballast. Ballast that has absorbed water will weigh more than dry ballast because water adds to the overall mass. The cleanliness of the ballast also plays a role; ballast-free of fine particles and debris will have a more consistent weight than ballast containing dirt and other contaminants.
Understanding these factors is crucial for railway engineers when calculating the ballast needed for a specific section of track. Ensuring the correct weight and distribution of ballast helps maintain the integrity and safety of the railway infrastructure, supporting the tracks and allowing for smooth and reliable train operations.
Railway Ballast Maintenance
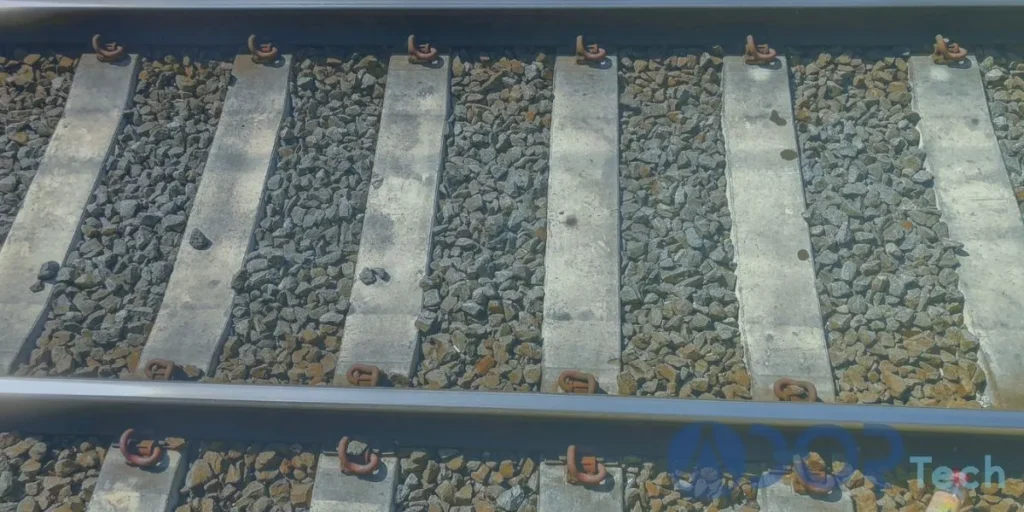
Maintaining railway ballast is crucial for ensuring the stability and longevity of railway tracks. Regular maintenance involves several key activities aimed at preserving the ballast’s effectiveness. One of the primary tasks is tamping, which involves using machines to lift the tracks and pack the ballast underneath the sleepers. This process helps restore the proper alignment of the tracks and ensures that the ballast is evenly distributed, providing optimal support.
Over time, ballast can become contaminated with fine particles, dirt, and debris, reducing its effectiveness. Therefore, cleaning the ballast is another essential maintenance activity. Specialized ballast cleaning machines remove unwanted materials, allowing the clean ballast to be reused. This process not only restores the ballast’s drainage properties but also extends its lifespan, reducing the need for frequent replacements.
Ballast renewal is sometimes necessary, especially in heavily trafficked areas where the ballast undergoes significant wear and degradation. During renewal, the old ballast is removed and replaced with new material. This process is often combined with track renewal projects to ensure the entire track structure is maintained to the highest standards. Regular inspection and monitoring are also critical components of ballast maintenance. Track engineers conduct visual inspections and use advanced technologies to detect any issues with the ballast, such as uneven distribution or excessive wear.
See also: “Sleepers Replacement Process“
By integrating these maintenance activities, railway operators can ensure that the ballast effectively supports the tracks, provides proper drainage, and reduces vibrations. Effective ballast maintenance is essential for safe and efficient railway operations, helping to prevent track-related issues and extending the lifespan of the railway infrastructure. Regular upkeep of the ballast ultimately contributes to the overall reliability and safety of the railway network.
Environmental Considerations for Railway Ballast
Sourcing and using railway ballast have several environmental impacts that need careful consideration. The extraction of materials like granite, limestone, and gravel for ballast involves quarrying, which can lead to habitat destruction, landscape alteration, and biodiversity loss. Quarrying processes also generate dust and noise, affecting local communities and wildlife. Additionally, transporting these heavy materials from quarries to railway sites contributes to carbon emissions, adding to the environmental footprint of railway construction and maintenance.
While railway ballast is beneficial for track stability and drainage, it also has environmental implications. Over time, ballast can become contaminated with pollutants such as oils, heavy metals, and other substances from railway operations. When it rains, these contaminants can leach into the surrounding soil and waterways, potentially harming local ecosystems. Proper management and disposal of old ballast are crucial to mitigate these risks. Recycling and reusing ballast can reduce the environmental impact by minimizing the need for new extraction and reducing waste.
Efforts to mitigate these impacts include adopting more sustainable quarrying practices, such as restoring habitats after extraction and using environmentally friendly transportation methods. Advances in ballast recycling technologies also significantly reduce the environmental footprint. By addressing these considerations, the railway industry can work towards more sustainable practices that balance operational efficiency with environmental responsibility.
Conclusion
In conclusion, railway ballast plays a vital role in ensuring trains’ safe and efficient operation. This seemingly simple layer of crushed stone or gravel is the foundation that supports the entire rail infrastructure. Without ballast, tracks would quickly become misaligned and unstable, posing severe safety risks.
Throughout this comprehensive guide, we have explored the various aspects of railway ballast, from its materials and properties to its functions in providing stability, drainage, vibration reduction, and load distribution. We have also delved into the crucial topics of ballast profile, weight, maintenance practices, and environmental considerations.
Maintaining the integrity of railway ballast is essential for the longevity and reliability of rail networks. Regular maintenance activities, such as tamping, cleaning, and renewal, ensure that the ballast performs its critical functions effectively. Adhering to industry standards and specifications further contributes to railway systems’ overall safety and performance.
As we look to the future, advancements in ballast materials, recycling technologies, and sustainable practices will play a pivotal role in minimizing the environmental impact of railway construction and maintenance. By understanding and appreciating the significance of railway ballast, we can better appreciate the intricate engineering behind the seamless operation of trains that connect our world.