Bogies are the undercarriage that connects the wheels to the vehicle’s body. They play a vital role in supporting the train’s weight, ensuring stability, and enabling smooth operation even on uneven tracks. The railway industry utilizes various types of bogies, including primary, secondary, and special-purpose bogies designed for specific train models and operational requirements.
The Bogie and Wheelset Wash Plant represents a breakthrough innovation in railway maintenance. It is a specialized system designed to clean and maintain the wheelsets and bogies effectively. The washing system thoroughly removes dirt, grease, and debris accumulated over time by employing advanced cleaning techniques, high-pressure water jets, and specially formulated cleaning agents. This meticulous cleaning process not only enhances the appearance of the bogies but also prevents corrosion, reduces wear, and prolongs the lifespan of the components.
This article delves into the world of bogie and wheelset cleaning in the railway industry, focusing on the revolutionary Bogie and Wheelset Wash Plant. Throughout the article, we will explore various aspects of bogies, their types, the significance/importance of washing them, and the different types of water and cryogenic bogie and wheelset wash systems available. Additionally, we will discuss the applications, benefits, and disadvantages of Bogie Wash Plants. Get ready to elevate your understanding of bogies, explore advanced wash systems, and unlock the keys to optimizing train performance. Take advantage of this enlightening read!
Understanding Bogies: The Backbone of Trains
Bogies are essential as the sturdy chassis or framework that supports and carries wheelsets, forming an essential modular subassembly of wheels and axles. They come in various forms depending on the mode of transport and are fundamental components in the transportation industry. Whether it’s rail cars, semi-trailers, road trains, or railway bogie exchanges, bogies are the reliable connection between the vehicle and its wheels.
In the railway context, bogies are commonly referred to as railroad trucks in North America and bogies in the UK. These structures provide axle attachment points, allowing the wheels to rotate smoothly via bearings. Rail vehicles like wagons, coaches, and locomotives rely on these robust bogies to ensure stable movement and weight distribution along the tracks.
Different modes of transport employ bogies with distinct characteristics. For instance, most rail and trucking bogies incorporate suspensions within their design to absorb shocks and vibrations, ensuring a smoother ride and better load distribution.
The versatility of bogies extends to their mounting mechanisms as well. Some bogies are mounted on swivels, offering rotational flexibility as seen in traditional railway carriages and locomotives. In contrast, others are jointed, sprung, or held in place using alternative methods, like the landing gear of an airliner or centerless bogies.
Understanding the role and design of bogies is paramount in the railway industry. Proper maintenance and care of these vital components contribute to trains’ safe and efficient operation. By providing stability, weight distribution, and load-bearing capabilities, bogies ensure optimal performance, passenger comfort, and the longevity of the rail vehicles.
In conclusion, bogies are the backbone of trains, providing the necessary framework and support for wheelsets. Their role in ensuring smooth movement, weight distribution, and stability is indispensable. By comprehending the significance of bogies, we gain insight into the intricate workings of trains and the essential maintenance practices needed to uphold their reliability and safety.
See also: “The Role of Train Wheelsets in Rail Transport“
Types of Bogies in the Railway Industry: Exploring Varieties and Functions
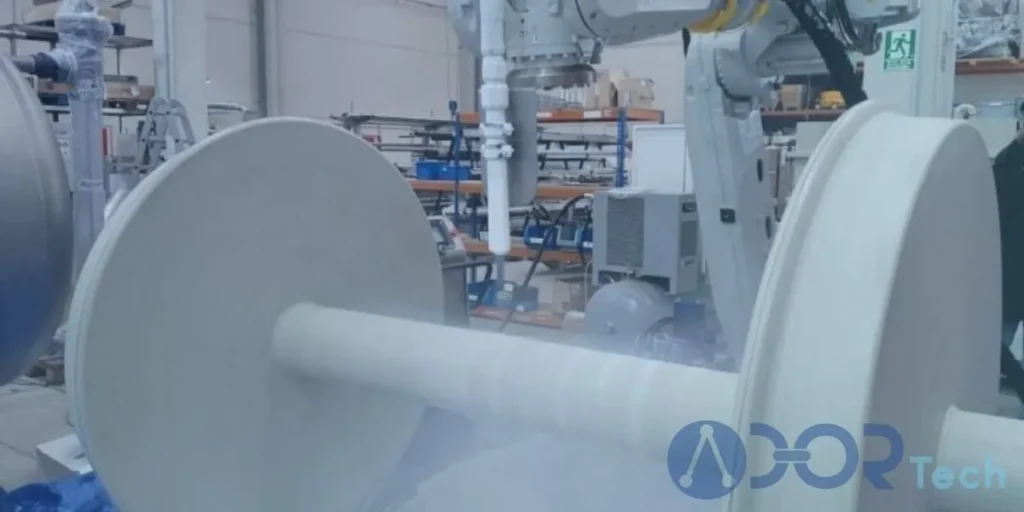
Various types of bogies are utilized in the railway industry, each designed to fulfill specific functions and accommodate different operational requirements. Understanding the diverse varieties of bogies is essential for efficient rail system design and maintenance. Let’s delve into some common types:
Primary Suspension Bogies: These bogies feature a suspension system that directly supports the weight of the rail vehicle. They often employ coil springs or air springs to absorb shocks and vibrations, ensuring a smoother ride and better passenger comfort.
Secondary Suspension Bogies: Secondary suspension bogies, or bolster-less bogies, incorporate a different suspension system between the rail vehicle body and the primary bogie frame. This secondary suspension further enhances ride quality, stability, and load distribution.
Special-Purpose Bogies: Special-purpose bogies are tailored to meet specific requirements for different train models or operational environments. For example, high-speed trains may utilize aerodynamic bogies designed to reduce air resistance, while freight trains may employ heavy-duty bogies capable of supporting heavy loads.
Bo-Bo Bogies: Bo-Bo bogies consist of two axles, each independently powered by an electric motor. These bogies are commonly used in electric locomotives and provide excellent traction and maneuverability.
Co-Co Bogies: Co-Co bogies consist of three axles, each powered by an electric motor. These bogies are typically in high-powered electric or diesel-electric locomotives, offering increased tractive effort and superior performance.
What is the Bogie and Wheelset Wash Plant?
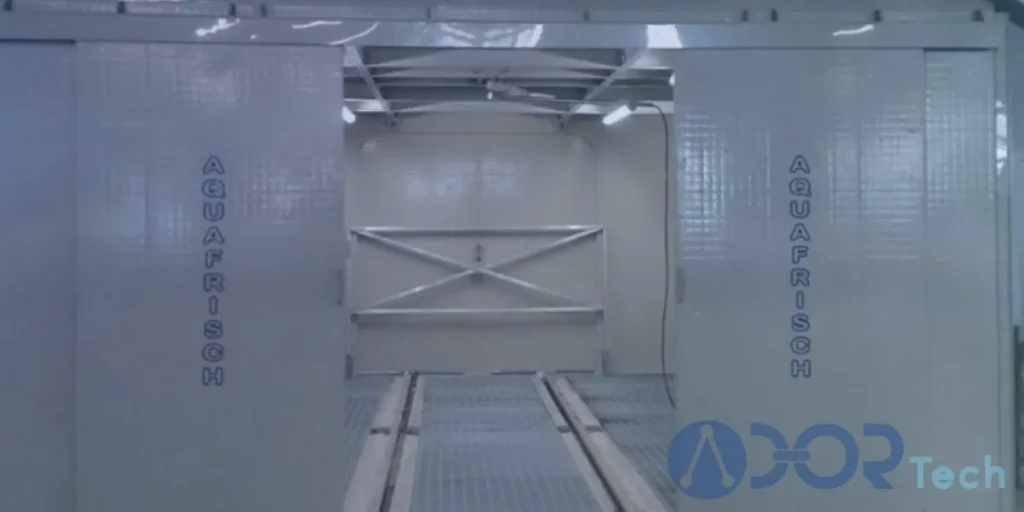
The Bogie and Wheelset Wash Plant is an advanced system designed for the automatic washing and rinsing of transit cars and locomotive bogies/trucks. These aqueous degreasing plants can clean bogies in various states of disassembly while they are still moving on their wheels.
The primary purpose of the Train Bogie Washing System is to effectively remove dirt, grease, and other contaminants from under gear parts of train coaches. By utilizing specially designed high-pressure oscillating spray jets, these plants ensure thorough cleaning while saving water and increasing the capacity and quality of the washing process.
This two or multi-stage cleaning system operates in a closed chamber, where bogies, wheelsets, and other rail car components are automatically cleaned. The compact design of the Bogie and Wheelset Wash Plant, combined with its aqueous-based cleaning process, enables efficient and reliable washing. The high-pressure water and oscillating spray jets achieve optimal cleaning results.
ADOR, a leading provider of railway maintenance solutions, offers different options for washing bogies. A hydro-cleaner can be used for manual washing of low quantities of bogies. However, for large quantities of bogies, an automated option is recommended. In this case, a gantry equipped with high-pressure nozzles and rotating heads moves along with the bogie, ensuring thorough and efficient cleaning.
In situations where bogies have sensitive areas that require careful handling, such as high-pressure sensitive components, ADOR suggests using robots. These robots can be programmed with unique washing paths to avoid sensitive areas, ensuring that the cleaning process is effective while minimizing the risk of damage.
See also: “Overview of the Train Wash System“
The Significance of Wheelset and Bogie Cleaning: Enhancing Performance and Longevity
The washing of bogies significantly enhances the performance and longevity of these components in the railway industry. As chassis or frameworks carrying wheelsets, Bogies endure various operating conditions and accumulate dirt, grease, and debris over time. Proper and regular cleaning using specialized systems like the Bogie and Wheelset Wash Plant is essential for maintaining their optimal performance.
By utilizing high-pressure water jets and specially formulated cleaning agents, bogie washing plants effectively remove dirt, grease, and other contaminants that can hinder the smooth operation of the bogies. This thorough cleaning process not only enhances the visual appearance but also prevents corrosion and reduces wear, contributing to the longevity of the bogies.
Regular washing of bogies also plays a crucial role in improving the overall performance of the railway system. Clean bogies ensure smoother rides by minimizing vibrations, reducing the risk of component failures, and enhancing passenger comfort and safety. Additionally, removing dirt and debris through washing helps maintain the proper functioning of sensitive components, such as brake discs.
Moreover, washing bogies using Train Bogie Washing System increases the capacity and quality of the cleaning process. These automated plants save water while ensuring thorough cleaning, allowing for efficient maintenance operations. By reducing the accumulation of dirt and grease, the washing process minimizes the need for frequent repairs and replacements, resulting in cost savings.
Types of Bogie and Wheelset Wash Systems
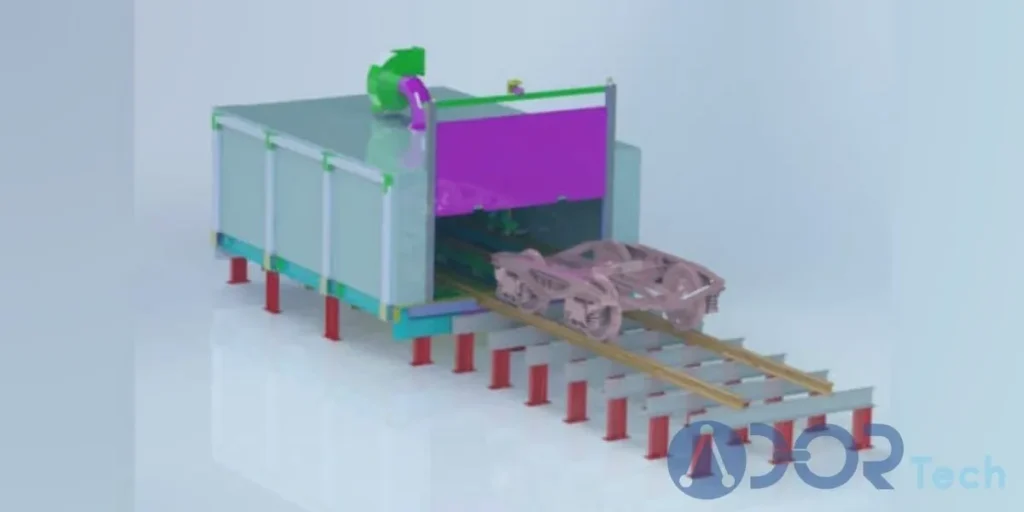
Various types of water, cryogenic bogie, and wheelset wash systems offer unique features and advantages for efficient and effective cleaning. Let’s explore three common types: Automatic Bogie Wash Cabins, Manual Bogie Wash Plants, and Robotic Bogie Wash Cabins.
Automatic Bogie Wash Cabins
Automatic bogie wash cabins are recommended for washing a large number of bogies. These cabins are constructed from stainless steel and feature a mobile arc fitted with high-pressure nozzles and rotating heads for thorough cleaning. Depending on the customer’s requirements, the cabin can have one or two doors for easy access or exit of the bogie.
Hot water is required in addition to detergent and high-pressure water to tackle heavy buildup on the bogies. These cabins include a storage tank and a water heating system, which can use electrical resistances or a diesel burner. Furthermore, they incorporate a water recycling system and steam recovery mechanism to optimize resources. Decalcification systems may also be included based on the quality of the main water. The control system allows for different washing programs, each with its duration, and is operated through a user-friendly touchscreen interface.
Manual Bogie Wash cabins
Manual bogie wash plants consist of polypropylene or stainless steel cabins equipped with access for the bogie and a door for staff entry. The washing process is carried out manually using a high-pressure washer. These plants feature a steam recovery system that condenses and recirculates the generated steam for reuse. They are suitable for washing smaller quantities of bogies.
Robotic Bogie Wash Cabins
Robotic bogie wash cabins combine automation and precision by integrating an industrial robot equipped with a high-pressure lance. Unlike conventional arc systems, the robot allows for specific control over the washing areas of the bogie. This optimization includes avoiding electrical or electronic zones through precise trajectory programming. The robots are mounted on self-propelled platforms for enhanced mobility.
Similar to automatic bogie wash cabins, robotic cabins include water recycling and steam recovery systems, as well as the option for decalcification based on water quality. The control system incorporates a touchscreen interface, providing intuitive operation and the ability to select different washing programs based on duration or specific washing areas.
In conclusion, the availability of different types of water and cryogenic bogie and wheelset wash systems allows tailored solutions to meet various washing requirements. Automatic bogie wash cabins offer high-capacity cleaning with configurable programs, while manual bogie wash plants are suitable for smaller quantities. Robotic bogie wash cabins provide precise control over washing areas and are ideal for avoiding sensitive zones. These wash systems promote resource efficiency and effective maintenance practices in the railway industry by incorporating water recycling, steam recovery, and decalcification systems.
Applications and Benefits of the Train Bogie Washing System
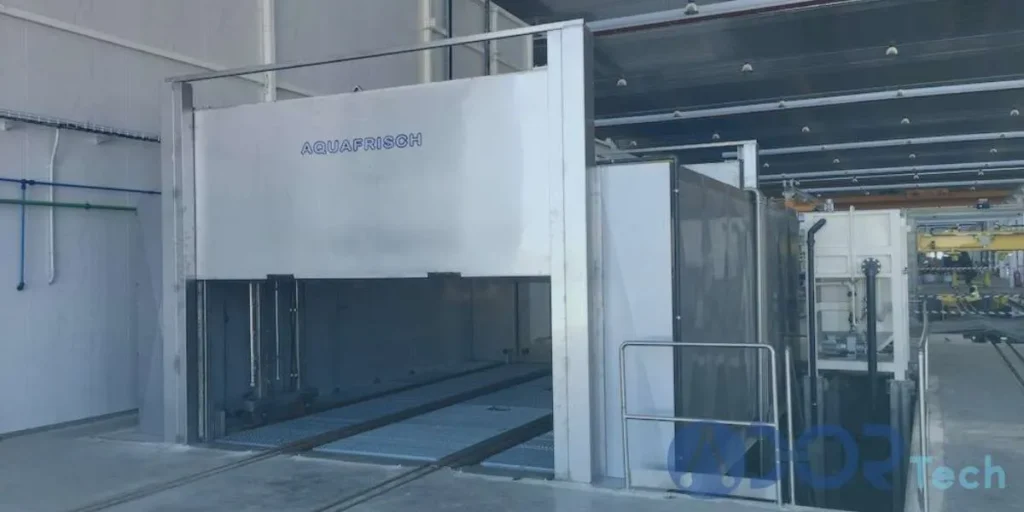
The train bogie washing system offers several applications and benefits essential in optimizing train performance and ensuring efficient railway operations. Let’s explore the key aspects and advantages of this system.
Applications
Transit Car and Locomotive Bogies: The train bogie washing system is specifically designed to automatically wash and rinse transit cars and locomotive bogies/trucks. It caters to various states of disassembly, allowing for effective cleaning even when the bogies are moving on their wheels.
Under gear Parts of Train Coaches: One of the primary applications of the bogie washing system is the thorough washing of under gear parts of train coaches. It targets dirt, grease, and other contaminants that accumulate on the bogies, ensuring a clean and well-maintained undercarriage.
Benefits
Enhanced Performance: Regular washing of bogies using the dedicated system significantly improves train performance. By removing accumulated dirt and grease, the system helps maintain optimal functionality and efficiency of bogies, ensuring smooth and reliable train operation.
Extended Lifespan: The train bogie washing system is vital in extending the lifespan of bogies and related components. Eliminating corrosive substances and contaminants helps prevent premature wear and tear, reducing the need for frequent repairs or replacements.
Improved Safety: Clean bogies contribute to enhanced safety in railway operations. Removing dirt and contaminants reduces the risk of malfunctions or failures, ensuring reliable and safe train journeys.
Water and Resource Efficiency: The bogie washing system incorporates water-recycling mechanisms, promoting water efficiency and responsible resource usage. By reusing water and implementing efficient water management systems, the system minimizes water consumption, reducing environmental impact.
Customized Washing Programs: The train bogie washing system offers customizable washing programs to cater to specific requirements. It allows users to configure different washing parameters, such as water pressure, cleaning agents, and duration, to ensure thorough and tailored cleaning for various bogies and under gear parts.
Time and Cost Savings: The automated nature of the bogie washing system saves time and reduces labor costs compared to manual cleaning methods. The system’s efficiency and effectiveness streamline the cleaning process, allowing for increased productivity and cost savings in railway maintenance operations.
Considerations Disadvantages of Train Bogie Wash Plants
While bogie wash plants offer numerous advantages regarding cleaning efficiency and maintenance optimization, it is essential to consider some potential disadvantages or limitations of these systems. Let’s explore a few considerations regarding the disadvantages of bogie wash plants.
Space and Infrastructure Requirements
Bogie wash plants typically require dedicated space within railway maintenance facilities. Installing wash plant equipment, water storage tanks, heating systems, and recycling mechanisms demands sufficient infrastructure and floor area. Limited space availability may make it challenging to accommodate these plants, particularly in older or smaller maintenance facilities.
Maintenance and Operational Costs
Operating and maintaining a bogie wash plant involves ongoing costs. These costs include regular equipment servicing, water treatment, energy consumption for heating, and periodic replacements of parts and consumables. Railway operators need to consider these additional expenses when evaluating the feasibility and long-term sustainability of implementing bogie wash plants.
Compatibility with Different Bogie Types
Bogie wash plants may not be universally compatible with all types of bogies used in the railway industry. Different train models or manufacturers may have variations in bogie designs, dimensions, or configurations, which could pose challenges in effectively fitting and cleaning certain bogie types within the plant. Therefore, compatibility and adaptability should be thoroughly assessed before implementing a specific bogie wash plant.
Training and Skill Requirements
Bogie wash plants require trained personnel who understand the system’s operation, maintenance protocols, and safety measures. Training employees or hiring skilled personnel to handle the equipment and processes can be an additional logistical and cost consideration for railway operators.
It is essential for railway companies to carefully assess these considerations and weigh them against the potential benefits when considering the implementation of bogie wash plants. Conducting a comprehensive cost-benefit analysis and evaluating the requirements and constraints of the railway maintenance facility will help make informed decisions regarding the suitability and feasibility of these systems.
Conclusion
In conclusion, bogie and wheelset wash plants have emerged as indispensable tools in the railway industry, revolutionizing train maintenance. These advanced cleaning systems offer a range of benefits that optimize train performance, enhance longevity, and improve overall operational efficiency.
Railway companies can appreciate maintenance’s crucial role in ensuring smooth and safe operations by understanding the significance of bogies as the backbone of trains; With different types of bogies in the railway industry, selecting the appropriate wash plant solution that caters to specific requirements and facilitates effective cleaning is essential.
Automatic bogie wash cabins, made of durable stainless steel, enable the automatic washing and rinsing of bogies using high-pressure nozzles and rotating heads. With hot water and detergent application, these plants effectively remove incrustations and grime, ensuring optimal cleanliness and performance. The versatility of these cabins allows for customization, with options such as one or two access doors to accommodate the specific needs of railway operators.
Manual bogie wash plants offer a practical and cost-effective solution for lower quantities of bogies. These cabins, constructed from polypropylene or stainless steel, provide a controlled environment for manual washing using high-pressure washers. Including a steam recovery system ensures efficient water usage and reduces environmental impact.
Incorporating robotics into bogie wash cabins takes maintenance precision to a new level. These automated systems utilize industrial robots equipped with high-pressure lances, allowing for targeted control over the washing areas. Robotic bogie wash cabins deliver efficient and tailored cleaning solutions by optimizing consumption and time and avoiding sensitive electrical or electronic zones. Self-propelled platforms further enhance the flexibility and maneuverability of these systems.
Water and cryogenic bogie and wheelset wash systems offer different approaches to cleaning. These innovative solutions use high-pressure water to remove contaminants and achieve superior cleanliness. With the inclusion of recycling systems and decalcification options, these systems address water conservation and quality concerns.
The applications and benefits of the train bogie washing system are vast. These wash plants optimize train performance by maintaining the integrity of bogies, ensuring smooth operation, and reducing the risk of breakdowns. By removing incrustations, grease, and other contaminants, these systems improve the longevity of bogies and associated components, resulting in significant cost savings over the lifespan of trains.
While bogie wash plants offer numerous advantages, it is crucial to consider certain disadvantages. Factors such as space requirements, maintenance costs, compatibility with different bogie types, and training needs should be thoroughly evaluated before implementing these systems.