
Brake Testing Equipment
Ensure precision testing for every critical rail component. Our railway test benches support comprehensive diagnostics for bogies, motors, and HVAC units. Engineered for efficient rolling stock maintenance, safety compliance, and long-term performance.
OVERVIEW
Our brake testing equipment is designed to test and evaluate the performance of railway products and components, especially in the production process, to ensure their reliability and safety. Using cutting-edge technology, it tests the brakes of single vehicles or complete trains either manually or automatically with a PC via radio or wireless remote control. Some of ADOR’s brake testing equipment features are as follows:
- GSM Connection for Remote Assistance
- Full Traceability of All Machine Parts
- PC Based Test Bench with Higher Flexibility Level
- Test Report
- Automatic Evaluation of Test Results
- Operation in Automatic and Manual Modes
- Quick Implementations, Changes, and Re-parameterizing
ADOR’s brake testing equipment is provided in various types as a solution to different companies’ systems:
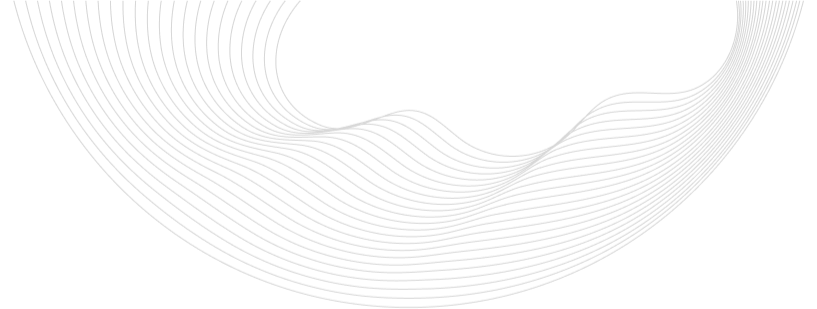

ModelS

Mobile Brake Testing

Valves Test Bench

Distributors Test Bench

Brake Cylinders Test

Brake Panel Test

Centralized Brake Test
Operational Features
ADOR’s brake testing systems are developed for precise, reliable, and repeatable evaluation of braking components used in rolling stock. Whether testing full train brake systems or individual valves and cylinders, each unit is equipped for both automatic and manual operation, with full traceability, remote assistance, and compliance to international and customer-specific standards.
The core operational features of each brake testing unit are listed below. For detailed configurations and integration options, please download the catalog at the bottom of the page.
Compliant with EN 60349-1 (DC) and EN 60349-2 (AC)
Periodic self-test on manometer chains for reliability
Pressure transducers with 0.125 percent full scale accuracy
Supports automatic tests and manual troubleshooting
Suitable for locomotives, wagons, and blocked train compositions
Tests a wide range of electric and pneumatic brake valves
Includes mechanical, pneumatic, and electrical interfaces
High flexibility control and test configuration via PC
0.125 percent full scale pressure transducers
Remote Support
Supports distributors from various manufacturers
High-accuracy transducers integrated into pressure vessel skid
PC-based test management with flexible configuration options
GSM connection for remote diagnostics
Automated test report and result evaluation
Tests brake cylinders with or without callipers
Configurable mechanical, pneumatic, and electrical interfaces
PC-based system with automatic and manual test options
Pressure accuracy of 0.125 percent full scale
GSM-enabled for assistance and updates
Complete brake system test managed by a single technician
Test can be conducted during loading phase, without locomotive
Delivers 3500 liters per minute at 10 barG
Compliant with ISO 8573-1 (2-3-2 class)
Connects via hose reels with FS hose for easy train interface
Designed to test brake panels in offline (bench) mode
Mechanical, pneumatic, and electrical setup for multiple panel types
PC-based system for automated and manual test cycles
0.125 percent full scale pressure transducers
Includes smart login, report generation, and full traceability
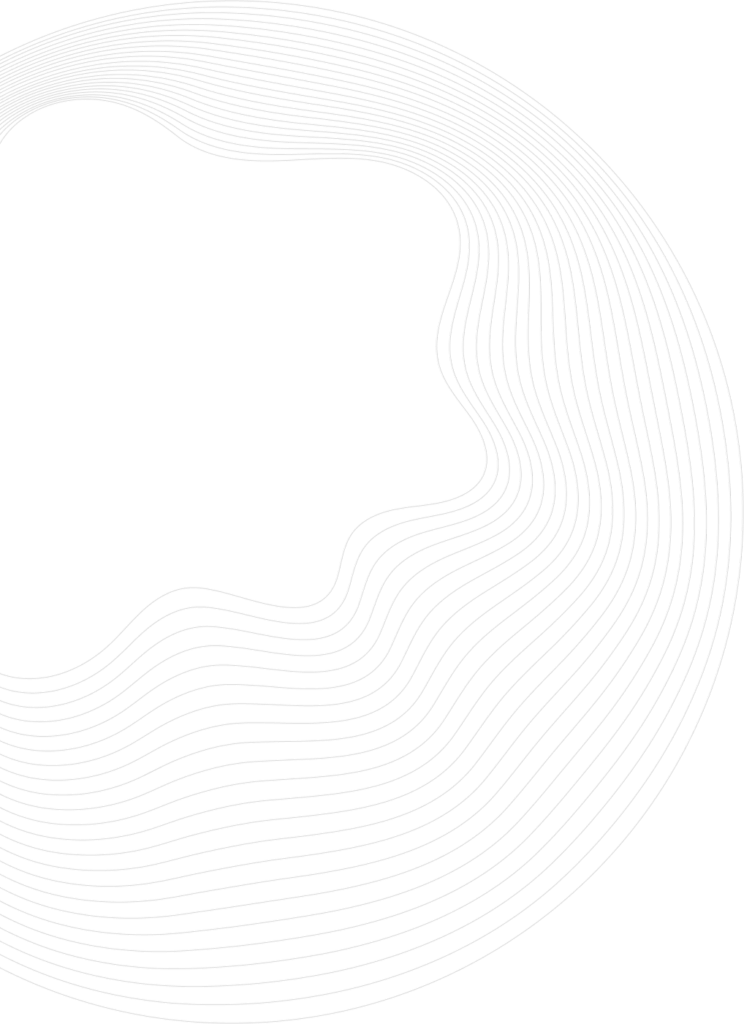
Gallery












Catalog
Please fill out the form to download the catalog:
Related Products

Test Benches
Various test requirements

Static Converters
Industrial environments or on mobile

Energy Storage System
For power applications
FAQS
Can one brake test system be used for different types of rolling stock components?
Yes. Brake testing systems are designed with flexible mechanical, pneumatic, and electrical interfaces. A single bench can often test multiple models or brands of valves, cylinders, or panels with minimal configuration.
Are the brake test benches compliant with international standards?
Absolutely. Most systems are compliant with UIC 540, UIC 543-1, and ISO standards. Additionally, they can be configured to meet local requirements like Trenitalia’s IT10006 and IT10027 or obtain certification from third-party bodies such as VIS.
How can I get more information?
Contact us for detailed technical documentation or tailored solutions to suit your project needs.
What is the scope of your work?
Our scope of work encompasses Canada and extends globally, offering tailored solutions for infrastructural and industrial needs.
What kind of support is available for these systems?
Support includes GSM-based remote assistance, on-site maintenance, calibration services, and optional upgrades or reparameterization. Many systems come with smart card access and diagnostics that allow remote troubleshooting and firmware updates.
Brake Testing Equipment for Rolling Stock: Ensuring Safety Through Precision Testing
In the railway sector, the brake system is arguably the most critical safety component of any rolling stock vehicle. Whether you’re dealing with locomotives, freight wagons, metro units, or high-speed trains, ensuring the proper functionality of every brake component is not optional—it’s a necessity. Railway depots and manufacturers rely on advanced brake testing equipment engineered for accuracy, repeatability, and compliance with international standards to meet this demand.
Brake test benches and mobile brake test units are designed to simulate real operating conditions in a controlled environment. This allows manufacturers and maintenance teams to assess performance, verify repairs, and confirm compliance with regulations before the rolling stock returns to operation.
In this article, we will explore what railway brake testing equipment is, why it’s essential, the different types available, and how to select the right solution for your needs.
What Is Railway Brake Testing Equipment?
Railway brake testing equipment refers to specialized systems designed to evaluate the functionality, air-tightness, responsiveness, and performance of train braking components. These components include brake cylinders, distributor valves, brake panels, air compressors, and complete train brake circuits.
The equipment is typically used in:
- Railway manufacturing facilities
- Maintenance depots
- Overhaul centers
- Certification laboratories
Using rail vehicle brake test systems, technicians can conduct functional tests, leakage assessments, response time evaluations, and electronic diagnostics on all relevant components. These systems support both manual and automatic testing modes and usually offer a PC-based interface with integrated data acquisition and reporting features.
Why Is Brake Testing Equipment Important in Rolling Stock Maintenance?
Testing ensures that all brake components meet operational and safety standards. A failure in any brake-related part can lead to operational delays, increased wear, or, in worst-case scenarios, serious accidents. By using dedicated train brake system testing solutions, operators gain measurable assurance that:
- The component functions as intended under load
- Pneumatic or electrical systems meet response requirements
- No leaks or deviations exist in the system
- Components meet national or manufacturer-specific standards (e.g., UIC 540, 543-1)
These checks support not only safety and compliance but also data-driven preventive maintenance and life cycle management.
Types of Brake Testing Equipment Used in Railways
Brake test systems can be classified by their scope and function. Some are designed for individual components, while others evaluate the system holistically.
Mobile Brake Testing Units
A Mobile Brake Testing Unit (MBTU) is used to assess the braking systems of entire trains, wagons, or blocked compositions. It is designed for portability and can operate independently from the locomotive. These units often feature:
- Automatic and manual operation modes
- HMI interface via Wi-Fi-connected PC
- Data logging with test reports
- Compliance with standards such as UIC 540 / 543
MBTUs are especially valuable in field environments, terminals, and yards.
Brake Valves Test Benches
A Brake Valve Test Bench evaluates a wide range of pneumatic and electric valves, including antiskid, check, relay, and isolation valves. These benches are built with adaptable interfaces and can simulate real pneumatic environments, ensuring the valve’s response, tightness, and functionality are validated.
Distributors Test Benches
These benches are used to test distributor valves from various manufacturers. Distributor valves play a key role in managing air flow during braking and releasing sequences. Leakage tests and functional tests are typically automated and results are stored digitally.
Brake Cylinder Test Benches
Brake cylinder benches are built to handle both cylinders with and without callipers. These devices ensure that air tightness and piston response are within the required tolerance. Accurate pressure sensors (typically 0.125 percent full scale) help validate performance under real operating conditions.
Centralized Brake Testing Systems
A Centralized Brake Testing System (CBTS) is ideal for managing full-train brake tests from a single operator station. These systems can conduct tests during the loading phase without requiring a locomotive. High air flow rates and pressure regulation ensure realistic simulations of braking behavior.
Brake Panel Test Benches
Brake panels combine several control elements into one interface. A Brake Panel Test Bench checks functions like electrical consumption, pneumatic reactivity, air tightness, and micro-switch response. These are typically used in workshop environments during component overhaul or after repairs.
Key Features to Expect in High-Quality Brake Test Benches
When evaluating brake testing equipment, certain features stand out as essential for long-term reliability and operator efficiency:
- PC-based control system with touchscreen interface
- Manual and automatic operation modes
- Pressure transducers with high accuracy (0.125 percent FS)
- Mechanical, pneumatic, and electric interfaces
- Barcode reader for component identification
- Remote diagnostics via GSM or Ethernet
- Automated report generation and result evaluation
- Compliance with customer-specific and international testing procedures
- Full traceability of test data and machine components
These features not only improve technician workflow but also reduce downtime and support quality audits.
How to Select the Right Brake Test System for Your Depot
Choosing the right system depends on several factors:
- Component Focus
Do you need to test brake valves, cylinders, panels, or the entire train system? Match the bench type to your operational needs. - Capacity and Volume
Consider how many components or vehicles you need to test per day or week. This will influence whether you choose a mobile system, single-station bench, or centralized platform. - Integration Requirements
Some depots need systems that integrate with CMMS platforms, fleet databases, or SCADA systems. Ensure the test bench supports the necessary protocols. - Environmental Conditions
If testing will be performed outdoors or in harsh environments, ensure the equipment has appropriate IP ratings and robust housing. - Compliance and Certification
Look for test benches certified by VIS or compliant with UIC and ISO standards to ensure regulatory compliance.
Conclusion
Investing in the right brake testing equipment for railways is not just about compliance—it’s about ensuring that every vehicle that leaves your depot is ready for safe operation. From component-specific benches to fully integrated test systems, there is a solution for every maintenance strategy and fleet type.
Whether you need to test brake cylinders, validate distributor function, or perform a full-train brake test, ADOR offers modular, scalable systems tailored to modern railway demands.
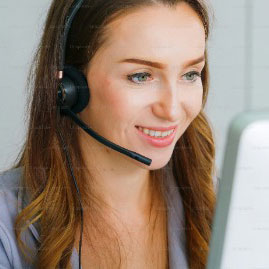