
Test Benches
Ensure precision testing for every critical rail component. Our railway test benches support comprehensive diagnostics for bogies, motors, and HVAC units. Engineered for efficient rolling stock maintenance, safety compliance, and long-term performance.
OVERVIEW
ADOR provides advanced railway test benches engineered to perform high-precision testing on a wide range of rolling stock components. Designed with cutting-edge technology, our systems ensure the safety, functionality, and compliance of key subsystems through reliable and efficient train component testing.
Each test bench is tailored for a specific application—such as bogies, motors, HVAC units, pantographs, and converters—allowing for focused diagnostics and optimized maintenance workflows. From depots to manufacturing lines, our rolling stock testing equipment supports both routine inspections and in-depth fault analysis.
Key Features:
- Automatic evaluation and test reports
- Full traceability of all machine parts
- Customizable protocols based on client needs
- Advanced control and monitoring systems
- Rapid re-parameterization and implementation
- Compliance with international and customer-specific standards
- GSM connectivity for remote diagnostics and support
Explore each of ADOR’s test benches for technical specifications and detailed capabilities.
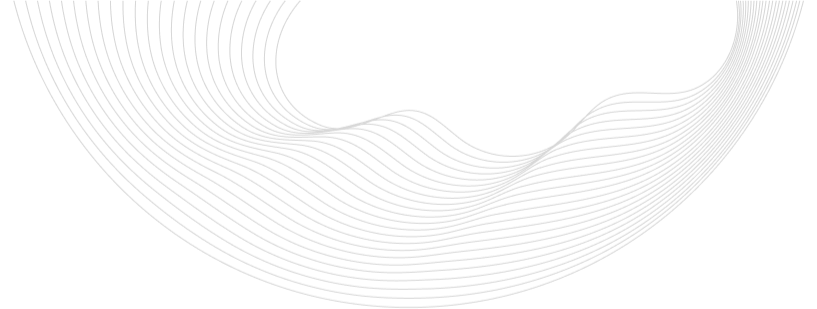

ModelS

Traction Motor

Pantograph

Door

Bogie Dynamic

Traction Convertor

Gearbox

Compressor

Coupler

HVTB
Operational Features
Each ADOR test bench is designed with flexibility, precision, and ease of operation in mind—tailored to meet the specific testing requirements of rolling stock components. Whether used for type testing, routine inspection, or post-maintenance validation, these systems support both manual and automatic operation modes and comply with industry standards.
The core operational features of this test bench are listed below. Please download the catalog at the bottom of the page for detailed configurations, optional modules, and integration capabilities.
Compliant with EN 60349-1 (DC) and EN 60349-2 (AC)
Short-time heat run, no-load, locked rotor, overspeed, optional load tests
Manual and automatic, depending on test type
Optional integration of vibration and temperature sensors
Designed for railway motor manufacturers and maintenance operators
CEI EN 50206-1 standard compliant
Static contact force, ADD, movement range, air tightness
Pneumatic and electric systems
Smart card login, remote support, and automatic test cycles
Automated test reports and customizable protocols
Follows EN 14752:2015 (where applicable)
Opening/closing, locking, obstacle detection, emergency operation
Includes control module, mock-up frame, and full instrumentation kit
Manual and automatic for type tests and diagnostics
Integrated report generation and full traceability
Motor and trailer bogies for high-speed, regional, and locomotive applications
Up to 300 km/h for motor bogies, 120 km/h for trailer bogies
Brake system tightness, signal acquisition, SCADA monitoring
Optional pressure, temperature, and vibration measurements
Full traceability with test reports and remote support
Traction and auxiliary converters, single modules
Includes resistive loads; inductive optional
Measures DC input, AC/DC output parameters
Integrated SCADA with manual and automatic modes
Smart card login, remote support, and test report generation
Parallel/perpendicular axis, with or without wheels and motors
Max input speed up to 6000 RPM, optional load tests
Optional vibration and temperature monitoring
Manual and automatic testing modes available
Suitable for gearbox and wheelset manufacturers and repair facilities
Air Generation Units with or without dryers
Flow rate, air tightness, temperature, insulation resistance
Support frame, vessel set, and safety features included
Semi-automatic and manual options
Soundproof cabin, dew point sensor, barcode reader
Pneumatic and electric couplers
Shutoff valve, air leakage, heating, extraction/retraction tests
Includes separate control and test modules
Manual and semi-automatic test options
Barcode integration, smart card login, automated reporting
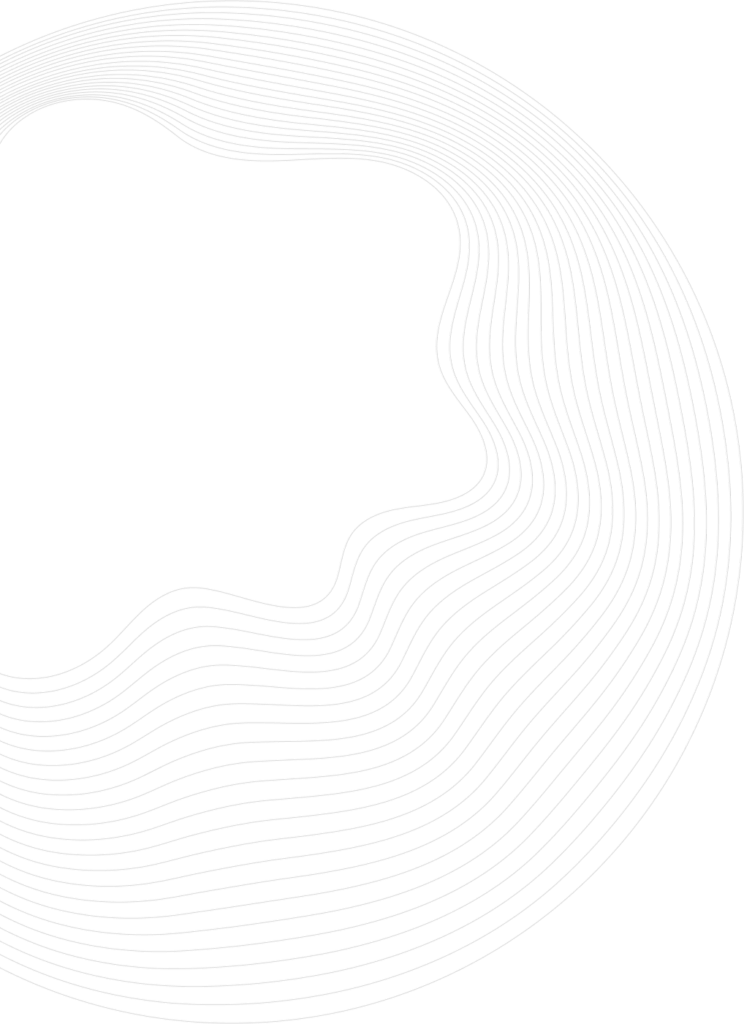
Gallery
















Catalog
Please fill out the form to download the catalog:
Related Products

Brake Testing Equipment
Highly functional and efficient

Static Converters
Industrial environments or on mobile

Energy Storage System
For power applications
FAQS
Are the test benches compliant with international standards?
Absolutely. Test benches are built to comply with applicable EN, CEI, or ISO standards (e.g., EN 60349 for motors, EN 14752 for doors, CEI EN 50206-1 for pantographs).
Do these systems support automated operation?
Yes. Most railway test benches support both manual and automatic operation modes, with programmable test protocols and automated result evaluation.
How can I get more information?
Contact us for detailed technical documentation or tailored solutions to suit your project needs.
What is the scope of your work?
Our scope of work encompasses Canada and extends globally, offering tailored solutions for infrastructural and industrial needs.
Can test benches be customized for unique rolling stock?
Yes. All benches can be configured for specific vehicle types or fleet requirements. Optional modules, software extensions, and component adaptors are available.
Railway Test Benches: The Foundation of Rolling Stock Quality and Safety
In the railway industry, precision, performance, and safety are non-negotiable. Every component—from a traction motor to a pantograph or door—must perform flawlessly under extreme conditions. To ensure this level of dependability, operators and manufacturers rely on specialized railway test benches.
These systems, designed to simulate real-world operating conditions, are critical for both production validation and maintenance verification. Whether testing gearboxes, motors, HVAC systems, or couplers, test benches for railway maintenance enable in-depth diagnostics that reduce downtime, prevent failure, and improve asset longevity.
In this article, we explore how rolling stock component test benches work, what types are available, and why they’re indispensable in modern railway operations.
What Is a Railway Test Bench?
A railway test bench is a dedicated testing system designed to simulate actual working conditions for various rolling stock components. These benches are typically used by:
- Manufacturers, to validate new components
- Depot operators, to verify post-maintenance performance
- Infrastructure managers, to ensure compliance with safety and operational standards
Test benches range from compact units for doors or HVAC systems to complex dynamic setups for bogies and traction motors.
Why Are Test Benches Essential for Rail Vehicle Maintenance?
Components in a rail vehicle are exposed to constant stress: vibration, electrical load, temperature fluctuations, and mechanical fatigue. A small defect left undetected can escalate into:
- Brake failure
- Traction power loss
- Airflow imbalance in HVAC systems
- Unexpected pantograph disengagement
- Improper door operation in passenger cars
Using rail vehicle testing equipment, operators can replicate operating conditions in a controlled environment. This allows early detection of wear, performance degradation, or safety-critical issues, long before they appear during service.
Common Types of Train Component Testing Systems
Each test bench is engineered for a specific purpose, offering detailed diagnostic capabilities tailored to the component being tested. Below are some of the most common train component testing systems available today:
Bogie Dynamic Test Benches
Simulates high-speed rotation, braking forces, and vibration profiles. These systems test motor and trailer bogies at speeds up to 300 km/h and provide measurements for pressure, temperature, and suspension dynamics.
Traction and Auxiliary Converter Test Benches
Used for validating power electronics such as GTO-based traction converters and auxiliary power units. These benches simulate electrical loads and assess voltage, current, and efficiency under variable conditions.
HVAC Test Benches
These replicate thermal and ventilation conditions to ensure HVAC units perform correctly under varying climate settings. Airflow, pressure, temperature, and condensation rates are measured across simulated zones.
Pantograph Test Benches
Test the force, stroke, and response of pantographs in static and dynamic conditions. They also assess air-tightness and response of the Automatic Dropping Device (ADD), critical for high-speed applications.
Gearbox Test Benches
Simulate load and speed conditions on gearboxes with or without attached wheels/motors. These systems detect gear tooth misalignment, vibration anomalies, and heat buildup during operation.
Coupler and Door Test Benches
Evaluate mechanical, pneumatic, and electrical functionalities of passenger and freight vehicle couplers and doors. Tests include emergency unlocking, obstacle detection, and force measurement.
Features of Advanced Railway Workshop Testing Equipment
Modern railway workshop testing equipment integrates high-performance hardware with flexible software. Key features include:
- Automatic and manual operation modes
- Integrated SCADA or HMI for monitoring and control
- Barcode readers and traceability tools
- Compliance with EN and ISO testing standards
- Remote diagnostics via GSM or Ethernet
- Customizable protocols per customer requirements
All test benches offered by ADOR and partners like IRMIE IMPIANTI are designed with these features in mind, ensuring compatibility with evolving rail technologies.
Where Are These Systems Used?
Test benches are typically installed in:
- Rolling stock manufacturing plants
- Railway Depot Workshops
- Heavy maintenance facilities
- Overhaul centers for freight and passenger fleets
They serve in both scheduled maintenance and condition-based maintenance programs, providing data for fleet lifecycle analysis and predictive upkeep.
Benefits of Implementing Rolling Stock Component Test Benches
Implementing test benches leads to:
- Fewer in-service failures
- Faster troubleshooting and component replacement
- Better quality control during manufacturing
- Reduced warranty claims and field service calls
- Compliance with international safety and maintenance standards
Additionally, automated test logging ensures results are easily stored, reviewed, and shared, supporting audits, quality management, and digital maintenance workflows.
Customization and Integration Capabilities
No two railway operators are the same. That’s why most modern test benches are designed for:
- Custom test cycles
- Plug-in modules for new component types
- Quick reparameterization for different training models
- Interfacing with depot IT systems
This ensures that investment in railway test benches remains future-proof and scalable as fleets evolve.
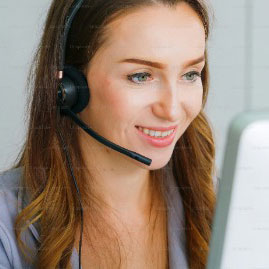