Ensuring that rail networks operate safely and efficiently is a crucial responsibility, and one key aspect of this is the regular catenary system inspection. The catenary system also called the overhead line equipment (OLE), comprises overhead wires that provide electric power to trains, enabling them to operate smoothly and dependably.
Inspecting the catenary system is a critical procedure that involves a thorough assessment of the different components of the OLE, such as the contact wires, support structures, and related hardware, to detect any potential defects, deterioration, or other issues that could compromise the system’s performance or pose safety hazards. Conventional inspection methods rely solely on human visual inspections and can be time-consuming, labor-intensive, and susceptible to inconsistencies.
Cutting-edge technologies have been used to develop advanced Overhead Wire Measurement Systems (OWMS) to tackle these challenges and improve inspection. These systems use various innovative methods, including machine vision, thermographic imaging, laser scanning, and drone-based inspections, to collect comprehensive data regarding the condition of the catenary system. Through these technology-driven inspection techniques, critical parameters and measurements can be acquired with unparalleled accuracy and efficiency. These encompass assessing wear and tear, monitoring clearances, evaluating tension and stagger, detecting faults and defects, and enabling effective condition monitoring and asset management.
Our advanced “overhead contact line monitoring system” helps detect faults before they become failures.
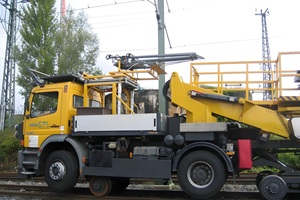
The catenary system inspection has various uses, including preventive maintenance planning, ensuring compliance with safety standards, improving operational efficiency and cost-effectiveness, and supporting informed life cycle management and asset planning decisions.
In this article, we will explore the complexities of inspecting catenary systems, delving into the basics of the system, the most recent inspection techniques and tools, critical inspection criteria and measurements, and the various uses of this essential process. We will also investigate the factors that impact catenary system inspection, such as environmental conditions, traffic volume, the age and condition of components, and regulatory standards. Additionally, we will examine future developments and advancements in this area, including incorporating the Internet of Things and sensor networks, extensive data analysis for proactive maintenance, independent inspections utilizing drones or robots, and the potential of augmented reality for inspection and training purposes.
What is a Catenary System?
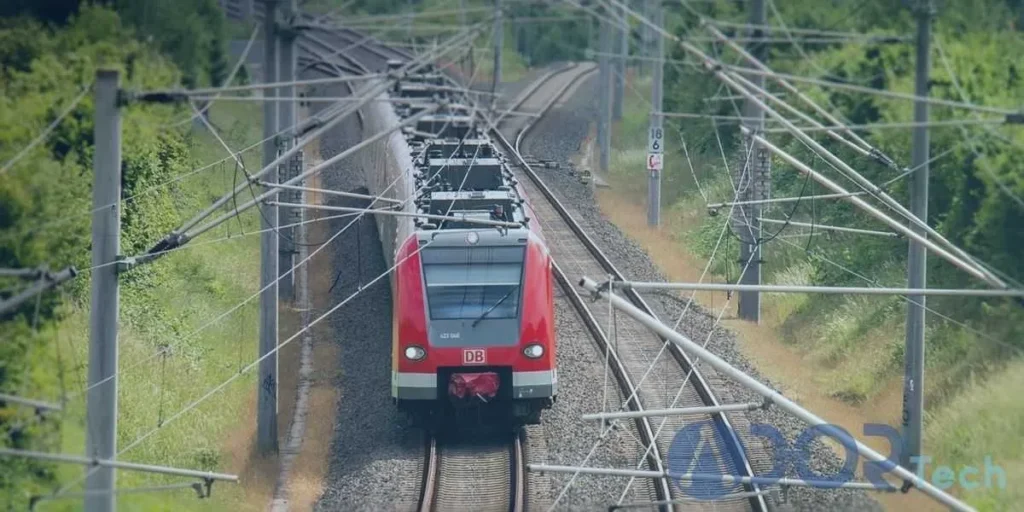
The catenary system, or the overhead line equipment, is a critical component of electrified rail networks. It consists of overhead wires that supply electric power to trains, enabling them to operate efficiently and reliably.
The system includes various essential elements. The contact wire, positioned above the rails, is the primary conductor for transmitting electrical energy to the train’s pantograph. Cantilevers, steady arms, and registration arms support the contact wire at strategic points along the track. Additionally, auxiliary wires such as the messenger and dropper wires provide structural support and help maintain the appropriate tension and stagger of the contact wire.
The catenary system significantly impacts modern rail transportation. It is essential for powering electric trains, which are environmentally friendly, energy-efficient, and capable of achieving higher speeds than diesel trains. Moreover, the system is crucial for ensuring the reliability and punctuality of rail services, as any disruption can lead to significant delays and operational challenges. Advanced Overhead Wire Measurement Systems (OWMS) are vital in inspecting the catenary system, identifying potential issues, and preventing significant problems.
See also: “Railway Overhead Line Equipment“
Potential issues and failure modes in catenary system
Catenary systems, which supply power to electric trains through the overhead contact wire, are prone to various issues and failure modes due to wear and tear, environmental conditions, and component defects. Regular inspections using advanced Overhead Wire Measurement Systems are essential for identifying and addressing these problems before they become major failures. Common potential issues and failure modes include:
- Wire wear and tear
- Clearance violations
- Tension irregularities
- Component defects (loosened bolts, broken insulators, damaged cantilevers)
- Pantograph wire breakage or disconnection
- Craters or abnormalities in the contact wire
- Vibration issues in the overhead line equipment
- Environmental factors (weather, vegetation growth, bird nesting)
- Misalignments or deviations from specified geometry tolerances
- Missing components in the catenary system
- Electrical arcing due to reduced wire cross-section
- Pantograph entanglement
- Infrastructure damage from wire breakages or requirements
- Power fluctuations or interruptions affecting train operations
Catenary system inspections using advanced Overhead Wire Measurement Systems can detect these issues by measuring wire thickness, height, and stagger and identifying any visible defects or anomalies. This enables timely maintenance and prevents major failures.
See also: “Railway Inspection and measurement systems“
Why is it important to inspect catenary systems?
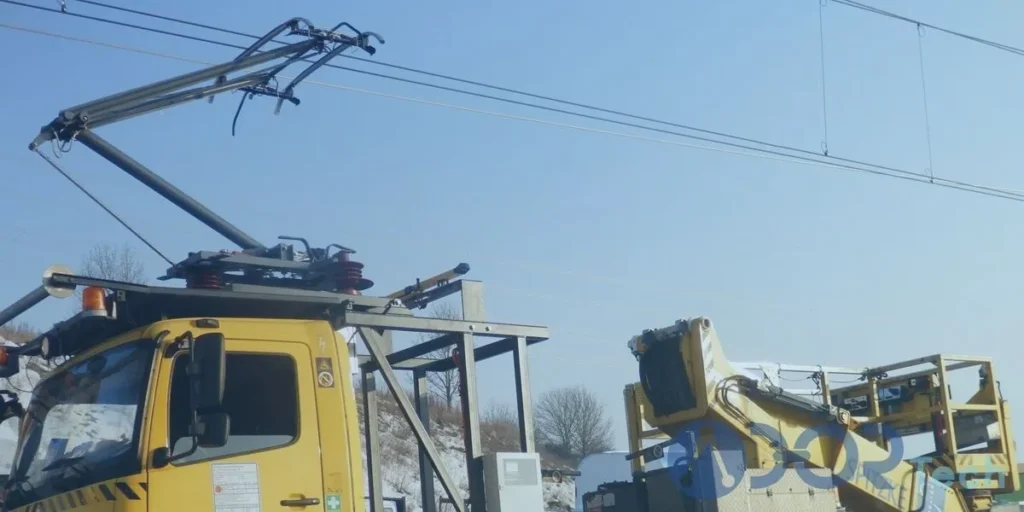
Frequent catenary system inspections are important to ensure the safe and effective functioning of electrified rail networks. These are the primary reasons why it is vital to inspect the overhead wire system:
1- Safety: The catenary system provides electric power to trains using a suspended contact wire above the rails. Safety hazards may arise from defects, misalignments, or wear in the system components. Regular inspections can prevent these issues from escalating into major incidents.
2- Operational reliability: Even minor deviations in the catenary system’s geometry can disrupt electric current flow to trains, causing power fluctuations, delays, and damage. Regular inspection minimizes operational disruptions.
3- Preventive maintenance: Regularly monitoring the catenary system components allows for timely preventive maintenance, avoiding breakdowns and saving costs in the long run.
4- Compliance and regulations: Rail operators and authorities have strict regulations for catenary systems. Regular inspections are essential for compliance and safe operations.
Catenary system inspection is essential for maintaining the safety, reliability, cost-effectiveness, and regulatory compliance of electrified rail networks, and it is facilitated by advanced Overhead Wire Measurement Systems. Timely identification of potential issues allows for prompt corrective actions to be taken, thereby ensuring the smooth and uninterrupted operation of rail services.
Improve safety and extend wire life with “overhead contact wire wear measurement“, perfect for preventive catenary system inspections.
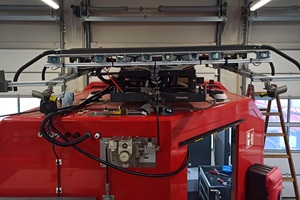
Consequences of Inadequate Catenary System Inspection
Regular and thorough inspections of the catenary system are crucial for the safe and effective functioning of electrified rail networks. Insufficient inspection methods can result in unnoticed problems in the overhead wire system, which may lead to severe failures and service interruptions.
One of the main dangers is the possibility of dewirement, which happens when the contact wire separates from the train’s pantograph. This could lead to extensive damage to the overhead line equipment over a considerable distance, not only presenting safety risks but also resulting in significant expenses for repairs and operational downtime.
Due to undetected wear and tear, clearance violations, or tension irregularities, the catenary system can experience electrical arcing, power fluctuations, or wire breakages. These issues can disrupt the flow of electric current to trains, leading to delays, service interruptions, and possible damage to traction equipment. Additionally, insufficient inspection of the catenary system could lead to failure to meet regulatory requirements and safety standards, putting certifications at risk and potentially subjecting rail operators to legal liabilities.
Conducting frequent inspections is essential to reducing these risks. Advanced technologies like machine vision, thermographic imaging, laser scanning, and ultrasonic measuring systems are utilized in these inspections to assess the catenary system components thoroughly. This enables early identification and correction of potential issues before they develop into significant failures.
Catenary System Inspection Methods and Tools

Methods and tools for inspecting catenary systems have evolved significantly to meet the critical need for thorough and dependable assessments of overhead line equipment. Cutting-edge technologies such as machine vision, laser scanning, and drone-based systems have transformed catenary system inspections. These Advanced techniques have revolutionized the evaluation of overhead wire measurement systems (OWMS), offering numerous benefits over traditional manual inspection methods. These benefits ensure improved safety, efficiency, and accuracy in assessing the condition of these crucial rail infrastructure components.
Visual Inspection Systems
Visual inspection systems utilize high-resolution area-scan cameras to capture detailed catenary component images. These systems have multiple strategically placed cameras to cover the entire inspection area, including cantilevers, contact wires, additional wires, and hanging posts in tunnels. The camera resolutions can vary up to 29 megapixels, providing an image resolution as high as 0.5mm per pixel. This level of detail enables accurate detection of defects such as loosened bolts, broken components, and even minor cracks or surface abnormalities.
Advanced image processing methods, such as structural analysis and feature-based detection algorithms, automatically recognize and pinpoint defects within the captured images. These systems often integrate post-detection modules using laser distance sensors to activate the cameras and lighting devices at precise locations relative to each catenary post, ensuring comprehensive coverage.
Laser Scanning Systems
Laser scanning systems utilize phase-shift measurement techniques to determine the height and stagger of overhead wires. These vehicle-mounted systems employ high-precision laser scanners that emit modulated laser beams toward the contact wire. By analyzing the phase shift between the transmitted and reflected signals, the system can accurately calculate the wire’s position. Overcoming challenges posed by varying wire reflectivity, electromagnetic interference, and environmental factors like sunlight and moisture, these systems can reliably measure the wire geometry even at high speeds. The laser scanning data is typically processed in real-time, enabling immediate detection of deviations from specified wire height and lateral position tolerances.
Ultrasonic Measurement Systems
Devices such as the OVHWizard utilize ultrasonic measurement methods to evaluate the position of the contact wire without physical contact. These systems operate based on the time-of-flight measurement principle, in which ultrasonic pulses are emitted from both ends of the device, reflected by the contact wire, and then detected by a central sensor.
By calculating the time, it takes for the pulses to travel to the wire and back, the system can determine the wire’s height and lateral displacement relative to the measurement device. This approach offers advantages over optical systems, as direct sunlight, reflections, fog, or mist do not affect it. The OVHWizard has an extendable measurement arm and an adjustable carriage, providing flexibility in positioning the device about the overhead line. The collected data is processed and presented graphically or in tabular format using specialized software applications.
Drone-based Inspection Systems
Uncrewed aerial vehicles (UAVs), commonly known as drones, play a significant role in inspecting catenary systems. Their ability to access hard-to-reach areas and collect detailed visual data on the condition of overhead line components is made possible by their high-resolution cameras, thermal imaging sensors, and other advanced equipment. This makes them valuable tools for efficiently and thoroughly assessing the state of infrastructure.
Integrated Systems
Some advanced OWMS combine various technologies, including visual inspection, laser scanning, and ultrasonic measurements, to offer a thorough evaluation of the catenary system. These combined systems frequently include robust data processing capabilities, allowing for real-time analysis and defect detection.
By utilizing advanced catenary system inspection methods and tools, rail operators can proactively detect potential issues, plan preventive maintenance, ensure safety compliance, and improve electrified rail networks’ reliability and operational efficiency.
Key Inspection Parameters and Measurements

Inspections of the catenary system, made possible by advanced Overhead Wire Measurement Systems (OWMS), include evaluating various important parameters and measurements to guarantee the correct operation and safety of the overhead line equipment. These parameters offer valuable information about the state of the catenary system components and assist in detecting possible issues before they become significant failures. The subsequent list outlines several crucial inspection parameters and measurements:
Wire Height
Monitoring the height of the contact wire is crucial for maintaining an optimal interaction between the overhead line and the train’s pantograph. Deviations from specified tolerances may result in excessive wear on the contact wire or the pantograph’s sliding surfaces, compromising current collection and potentially causing dewirements. OWMS technologies, such as laser scanning and ultrasonic measurement systems, are used to precisely measure and assess the contact wire height along the entire line’s length.
Wire Stagger (Lateral Position)
The position of the contact wire about the track centerline, known as stagger, is an essential factor that needs to be maintained within specific limits. If the stagger is too great, it can cause the contact wire to slide off the sides of the pantograph, leading to disconnections and potential damage to the overhead line equipment. Advanced overhead wire monitoring systems can accurately measure the stagger using laser scanning and ultrasonic measurements, allowing for timely adjustments to prevent serious failures.
Wire Thickness (Wear)
Monitoring the thickness of the contact wire is essential to detect areas of excessive wear caused by the pantograph’s interaction. Over time, this wear can increase the risk of wire breakages or electrical arcing. Some OWMS, such as the ATON system used by the Netherlands Railways, utilize specialized telescopic systems and laser-based measurement methods to evaluate the wire thickness across the entire catenary network precisely.
Clearance Measurements
Ensuring enough space between the overhead line parts and other structures like bridges or tunnels is crucial for safe and continuous rail operations. OWMS can offer precise clearance measurements, enabling proactive detection and resolution of possible clearance breaches that may result in equipment damage or operational interruptions.
Tension Monitoring
Maintaining consistent tension in the contact wire is essential to ensure even current collection and reduce wear. OWMS can constantly monitor these factors, identifying any abnormalities resulting from conditions like thermal expansion or mechanical stress. This data is precious for preemptive maintenance and averting possible problems such as excessive sagging or arcing.
By conducting thorough evaluations of these essential factors during advanced catenary system inspections, rail operators can guarantee the secure and dependable functioning of their electrified networks, streamline maintenance activities, and prolong the lifespan of the overhead line equipment.
Factors Influencing Catenary System Inspection
Catenary system inspections can be affected by various factors that can influence the inspection procedure’s precision, dependability, and effectiveness. It is important to comprehend and deal with these factors to guarantee thorough and efficient evaluations of the overhead line equipment. Several important factors that influence catenary system inspections include:
1- Environmental Conditions:
Adverse weather, like rain, snow, fog, or direct sunlight, can affect inspection technologies. Visual inspection and laser-based measurements may be hindered by poor lighting or obstructions from precipitation or atmospheric conditions. These factors less impact ultrasonic measurement systems, such as the OVHWizards, as they use ultrasonic pulses for measurement instead of optical signals.
2- Traffic Density and Usage Patterns:
The frequency and intensity of rail traffic on a route can impact the wear and degradation of the catenary system components. High-traffic routes may need frequent inspections to detect issues promptly and prevent service disruptions. Coordinating inspections with operational schedules is essential to minimize interference with regular rail services.
3- Age and Condition of Catenary Components:
The age and condition of overhead line equipment determine the frequency and scope of necessary inspections. Older or heavily used systems may require more frequent and rigorous inspections to monitor for accelerated wear or potential failures.
4- Regulatory Requirements and Standards:
Catenary system inspections are subject to varying standards and guidelines by different rail operators and regulatory bodies. Compliance with these regulations is crucial for ensuring rail network safety and interoperability.
5- Vehicle Dynamics and Stability:
The dynamics and stability of the inspection vehicle can affect the accuracy of catenary system inspections. Factors such as vehicle roll, suspension characteristics, and track gauge variations can introduce measurement errors if not properly compensated. Advanced OWMS often incorporate roll compensation mechanisms and vehicle movement correction algorithms to enhance measurement precision.
Conclusion
Regular and thorough inspections of the catenary system are crucial to ensure that electrified rail networks operate safely, reliably, and cost-effectively. Overhead Wire Measurement Systems utilize cutting-edge technologies such as machine vision, laser scanning, ultrasonic measurements, and aerial drones to inspect these crucial overhead power line components with exceptional precision and efficiency. By closely monitoring parameters such as wire height, stagger, thickness, clearances, and tension, potential issues can be identified early, preventing them from developing into significant failures that could compromise safety and disrupt service.
Environmental conditions, traffic levels, component age and condition, regulatory standards, and vehicle stability are crucial for conducting thorough OWMS inspections. Overcoming these challenges is crucial for maximizing the value of OWMS data to inform corrective maintenance, replacement planning, and other life cycle management decisions for the catenary system assets.
As railway networks grow and the number of passengers increases, OWMS inspections will become increasingly important for maintaining performance and prolonging the lifespan of these essential electrification systems. Incorporating IoT monitoring, augmented reality visualization, and automated defect recognition can lead to even more significant improvements in safety and productivity. A proactive inspection approach utilizing OWMS technology is crucial for modern railway operators to ensure the public receives reliable and safe electric train services.