Railroads are the lifeblood of supply chains, transporting goods and materials across vast distances. However, maintaining thousands of miles of railroad track is a monumental task. An indispensable tool has emerged to aid in this continuous upkeep: the railroad excavator. Specially engineered for the rigors of railroad maintenance, these heavy-duty machines allow crews to repair, replace, and upgrade track infrastructure efficiently.
This article explores the world of railroad excavators, focusing on their unique features that are optimized for track maintenance. It delves into the different types of railroad excavators, highlighting the attachments and functionalities that enable efficient debris removal, ballast distribution, and handling rail and tie replacements. The discussion also includes the benefits of using railroad excavators in enhancing safety and efficiency during rail maintenance tasks.
In outward appearance, railroad excavators resemble their counterparts used on construction sites. However, customized designs make them indispensable for smooth railroad operations. With their unique capabilities, railroad excavators have become essential equipment for modern track maintenance. Their engineering allows rail workers to keep supply lines open across vast interconnected networks safely. Railroad excavators are the powerhouse machinery that keeps trains rolling smoothly daily.
Tackle rail and roadside tasks with one machine; our “hi-rail loader” offers unmatched flexibility for drainage, lifting, trenching, and more.

What are Railroad Excavators?

Railroad excavators, also called road-rail excavators, are versatile heavy machinery designed specifically for construction and maintenance tasks on rail tracks. Blending the capabilities of a wheeled excavator with customized features for traveling on rails, railroad excavators can traverse right along the tracks they are working on. This allows them to perform a wide range of railroad infrastructure jobs safely and efficiently.
At their core, railroad excavators utilize much of the same technology as a wheeled model. The main body houses the operator cab, engine, and pump systems to power the hydraulic arm and attachments. But railroad excavators have sturdy steel wheels mounted on specialized axles that enable them to grip and ride along rail tracks firmly. The separate hydraulic system driving the rail wheels provides precise maneuvering directly on the rails.
This rail mobility lets railroad excavators carry out tasks like excavating and backfilling soil, grading, and reshaping track beds, clearing ballast, and hauling, lifting, and placing ties, rails, and other materials. Interchangeable attachments like tie handlers, tampers, and rail layers optimize them for each job. Their robust construction withstands the jolts and vibrations inherent to daily operations on rail lines.
With their dual-mode mobility and versatile attachments, railroad excavators are ideal all-purpose tools for railroad builders and maintenance crews. They combine the off-track versatility of an excavator with specialized rail capabilities for efficiently constructing, inspecting, and repairing rail networks.
See also: “Railway Maintenance Equipment“
Railroad Excavator Applications in the Railway Industry
Railroad excavators have become indispensable machines in the railway industry due to their unique capabilities that optimize them for railroad construction and maintenance demands. Thanks to their dual-mode mobility to traverse both on and off tracks, railroad excavators can access job sites and move seamlessly along rail lines to carry out essential track maintenance tasks.
One of the most common uses of railroad excavators is ballast maintenance. Their powerful hydraulic arms and ballast buckets, and attachments allow them to dig, rake, redistribute, and replace the crushed rock ballast that forms the track bed efficiently. This routine maintenance keeps the tracks properly supported and drained for trains. Railroad excavators are also critical for inspecting and repairing rail tracks. Attachments like tie handlers give them the skill to remove and install new railroad ties and rails as needed to maintain smooth tracks.
For new railroad construction, railroad excavators prepare the terrain alongside tracks with their excavation capabilities. Their precise operation on rails allows them to unload and set down ties and rails to expand lines. Railroad excavators can also install other track components, like signals or electronic sensor,s along the new rail. With specialty wheel attachments, they can even act as compactors to pack down terrain alongside expanded routes.
Whether maintaining hundreds of miles of existing track or building new rail networks, railroad excavators tackle these demanding jobs with their unique power, precision, and rail mobility. They have proven to be a versatile and efficient backbone of the modern railway industry.
What Are the Advantages of Railroad Excavators?

Railroad excavators provide significant benefits for railroad construction and maintenance work. The essential advantage is their dual-mode mobility – they can travel and operate on and off railroad tracks. This provides convenient access to worksites without needing separate machines or equipment transport. Sturdy rail wheels built into the excavator undercarriage allow them to traverse along rail lines smoothly. Yet they retain the ability to travel and maneuver like a standard wheeled excavator when off the tracks.
Their specialized engineering and robust construction make railroad excavators ideal for the demanding conditions of daily operation on rail beds. Functions like electronic swing and lift limits provide precise control to avoid contacting overhead wires or other rail infrastructure. The arm articulation and interchangeable attachments facilitate lifting, moving, and installing heavy track components. Solid frames and stabilizers counteract the shaking and jostling inherent when working and traveling on railroad ballast.
Railroad excavators improve work efficiency compared to general excavators or bring in separate rail-capable equipment. A single railroad excavator combines the versatility to excavate, haul, lift, and place track materials. Rapid, direct travel between worksites on rail reduces non-productive transport time. Their capabilities enhance productivity for tie replacement, rail laying, ballast clearing, and other critical maintenance activities.
With their dual-mode mobility, specialized engineering, and versatile attachment capabilities, railroad excavators have distinct advantages over other railroad construction and maintenance equipment. Their unique optimization for rail work makes them indispensable tools for smoothly operating and expanding freight and passenger rail networks. Railroad excavators enable crews to work safer, smarter, and more efficiently along the rails.
What Are the ADOR’s Railroad Excavator Types?

The road-rail excavator loader models are explicitly engineered for mobility and work capabilities on rail infrastructure. ADORTech offers several purpose-built railroad excavators in varied sizes and configurations to suit various rail applications.
The Enzo is a heavy-duty road-rail excavator loader. With a 217 HP diesel engine and robust frame, the 29,300 kg (about 64595.37 lb) Enzo is designed for demanding railroad construction and maintenance tasks. It has a maximum lift capacity of 10 tons and a 360-degree continuous rotation angle for its work equipment. The Enzo can accommodate various rail attachments like tie handlers, ballast buckets, rail layers, and tampers. Its power and attachment versatility make it ADORTech’s flagship railroad excavator for significant track-building and rehab projects.
See also: “Hi-Rail Excavator Attachments“
For a more compact size while retaining rail capabilities, ADORTech offers the GF13 and GF22 models. The lighter GF13 at 13,680 kg (about 30159.2 lb) is suited for narrow gauge networks and light-duty maintenance, providing agile maneuverability in tight spaces. The 16,600 kg (about 36596.69 lb) GF22 delivers a balance between power and compact size, with the speed to move down the rails quickly between worksites. Both models accept tools like buckets, magnets, and grapples to clear debris and access tight areas.
J882 road-rail excavator loader is designed for optimal versatility. Its 200 HP engine and 25,500 kg (about 56217.81 lb) weight combine robust lifting power with rail mobility to serve as either a rail excavator or an off-track excavator. The J882 accepts all the typical railroad attachments like tie handlers and tampers. Its versatility makes it suitable for general construction and industrial material handling applications.
These road-rail excavator models represent some of ADORTech’s extensive equipment offerings engineered for railroad applications. Their different sizes, capabilities, and attachments provide customized solutions for rail construction or maintenance needs. ADORTech’s partner (La Falco) specialty is building innovative, purpose-built railroad excavators that deliver safety, productivity, and reliability for the most demanding rail projects.
Railroad Excavators’ Technical Specifications
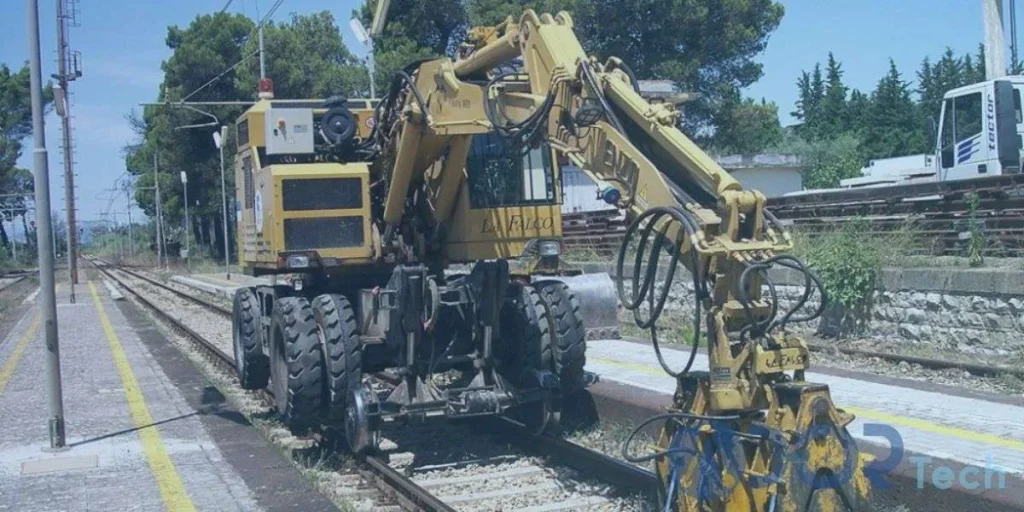
Railroad excavators have customized technical specifications optimized for mobility and work duties on rail infrastructure. While sharing similarities with traditional excavators, critical differences in their engineering improve their capabilities on the rails.
A primary specification is their wheel systems – road-rail excavators have sturdy steel rail wheels added to their undercarriage. These powered rail wheels, which can be disengaged to allow regular rubber-tire travel, enable the excavators to roll along rail tracks stably. The steel wheels are flanged to grip the rails, and the front and rear rail axles can pivot slightly to better align with the track.
Road-rail excavators need high-horsepower diesel engines to provide ample power for rail travel and heavy material movement. Engines in the models range from 95 kW (130 HP) for the compact GF13 to 217 HP for the robust Enzo. The engines utilize features like turbocharging and pilot control systems to develop maximum torque while minimizing fuel consumption.
The hydraulic systems onboard these excavators feed powerful hydraulic rams for lifting, rotating, and manipulating rail work attachments. Models like the Enzo and J882 use advanced ‘PentaHydra’ systems – multiple independent hydraulic circuits that allow simultaneous operation of the arm, travel, and attachment functions. The sizeable hydraulic oil reservoirs supply fluid for attachment tools like rail tampers or pile drivers.
Purpose-built rail excavators have sturdy, reinforced frames and counterweights engineered to withstand daily railroad operation jolts, vibrations, and dynamic loads. Their low centers of gravity and wide gauge rail axles enhance stability when traveling on uneven ballast or performing material lifts. Safety features like overhead proximity sensors prevent contacting electrified catenary wires.
The operator cabs provide optimal visibility, ergonomic controls, and sound insulation against engine and rail noise. Their swiveling seats and wrist rest reduce fatigue from long hours operating on the rails. Some models offer dual-operator cabs for a trainee or assistant.
These excavators can utilize a variety of quick-change attachments suited for rail tasks like ties and debris grapples, rail grab/laying arms, ballast forks, and tampers. Standard buckets can be swapped for specialized rail work tools in the field.
In summary, purpose-built railroad excavators integrate heavy-duty engineering specifications tailored for safe, efficient mobility on railroad tracks. Their specialized technical capabilities allow rail owners to use diverse, highly productive equipment to maintain and expand their networks.
Conclusion
Railroads form the backbone of our transportation infrastructure, connecting suppliers, manufacturers, and consumers across continents. But keeping these vast rail networks running smoothly is an endless task. As we have explored, an essential tool has emerged to take on this monumental job – the railroad excavator. Purpose-built railroad excavators integrate capabilities that optimize them for track maintenance and construction. Their specialized mobility allows them to traverse rails like a locomotive while retaining off-track maneuverability. Custom attachments provide the versatility to clear ballast, install ties, and rehab infrastructure. Robust frames and stabilizers withstand the punishing conditions inherent to daily operation on uneven track beds.
Models like the Enzo and J882 represent the pinnacle of engineering for rail-capable machinery. Major rail operators continue to add these modern excavators to their maintenance fleets, retiring older converted excavators. The efficiency gains provided by machines engineered from the ground up for rail work are too substantial to ignore. As railroads carry more freight and passengers year after year, demand for productive and reliable maintenance equipment will continue. Railroad excavators enable smaller crews to cover more miles of track while achieving higher-quality repairs and upgrades. Integrating the latest technology, like GPS positioning and sensor-enhanced automation, will further improve their capabilities.